Silicone Membrane for Vacuum Press - A Game Changer in Various Industries
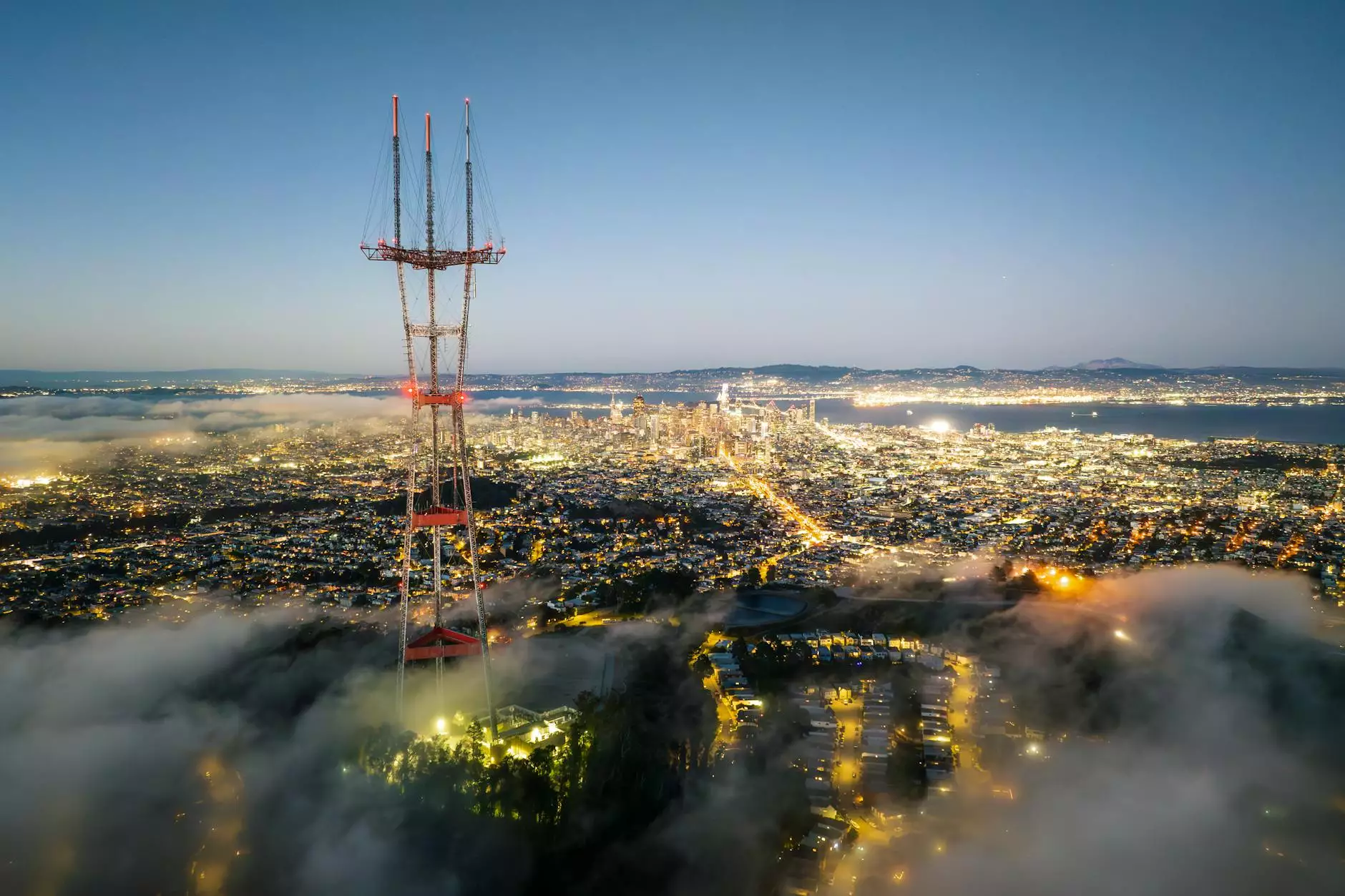
In today's fast-paced world, businesses in the Health & Medical, Beauty & Spas, and Medical Spas sectors are constantly seeking innovative solutions to enhance their processes. One such revolutionary product that has gained traction is the silicone membrane for vacuum press. This article delves into the manifold benefits of silicone membranes, their applications, and why they are becoming indispensable in various industries.
What is a Silicone Membrane?
A silicone membrane is a flexible, durable material designed to withstand pressure and temperature fluctuations. Its unique properties make it ideal for vacuum presses, which are used in a plethora of applications ranging from product manufacturing to healthcare. The silicone membrane for vacuum press not only provides a tight seal but is also resistant to a variety of substances, making it suitable for both industrial and consumer use.
The Importance of Vacuum Presses
Vacuum presses are essential tools in multiple industries, primarily because they offer the ability to create airtight seals. This capability is crucial for processes such as:
- Composite Material Manufacturing: Used extensively in aerospace and automotive sectors.
- Woodworking: Ideal for laminating surfaces and creating high-quality finishes.
- Food Packaging: Ensures freshness and prolongs shelf life.
- Medical Applications: Ensures sterility in product packaging.
Benefits of Silicone Membrane for Vacuum Press
The adoption of silicone membranes in vacuum presses presents several key advantages:
1. Enhanced Durability
Silicone membranes are resistant to tears and punctures, providing a reliable option that lasts longer than traditional materials. This durability ensures less downtime for maintenance and replacements, thereby increasing operational efficiency.
2. Temperature Resistance
Operating in extreme temperatures is commonplace in many industries. Silicone membranes can withstand a wide range of temperatures, ensuring that processes remain uninterrupted despite environmental changes.
3. Chemical Resistance
In settings where exposure to chemicals is inevitable—such as in medical or beauty applications—silicone membranes resist degradation, making them a safer and more practical choice.
4. High Flexibility
The inherent flexibility of silicone allows for seamless fitting and operation within vacuum presses of various designs. This characteristic facilitates the production of complex shapes without compromising quality.
5. Easy Maintenance
Silicone membranes can be cleaned easily, which is crucial in both medical and beauty applications where hygiene is paramount. Their non-porous surface prevents the accumulation of dirt and bacteria, ensuring a sterile environment.
Applications in Health & Medical Industries
In the Health & Medical sector, the silicone membrane for vacuum press plays a pivotal role in several applications:
- Pharmaceutical Packaging: Ensures the integrity of medications through vacuum sealing, prolonging their effectiveness.
- Medical Device Manufacturing: Used to create precision components that require airtight sealing.
- Bioscience Research: Assists in applications that require controlled environments to promote accurate research and testing.
Applications in Beauty & Spa Industries
The Beauty & Spas industry has also embraced silicone membranes in vacuum presses. Here’s how:
- Product Packaging: Ensures beauty products are kept fresh and free from contamination.
- Cosmetic Treatments: Used in facial therapies and body treatments to enhance results by maintaining a vacuum to manipulate skin and tissue.
- Equipment Manufacturing: Vital in creating spa equipment that requires precision and durability.
Applications in Medical Spas
In Medical Spas, silicone membranes enable the provision of specialized treatments effectively:
- Aesthetic Procedures: Used to create systems for effective delivery of therapeutic agents through vacuum methods.
- Skin Care Treatments: Enhance various skin treatments by ensuring optimal conditions for active ingredients.
How to Choose the Right Silicone Membrane for Vacuum Press
Choosing the right silicone membrane for vacuum press is crucial for ensuring optimum performance. Here are some factors to consider:
1. Thickness and Size
The thickness of the silicone membrane will impact its resistance and flexibility. Consider the specific requirements of your vacuum press to select the appropriate size.
2. Temperature Tolerance
Depending on your industry’s needs, ensure that the silicone membrane can handle the temperature range expected in your processes.
3. Chemical Compatibility
Assess the chemicals the membrane will come into contact with, ensuring that the silicone is resistant and won’t degrade over time.
4. Maintenance Needs
Select membranes that are easy to clean and maintain, particularly in medical or beauty applications where hygiene is a priority.
5. Manufacturer Reputation
Source your silicone membranes from reputable manufacturers. Look for quality certifications and customer testimonials to guarantee reliability.
Conclusion
The versatility and advantages of the silicone membrane for vacuum press make it an invaluable tool across various industries, including Health & Medical, Beauty & Spas, and Medical Spas. With its durability, flexibility, and chemical resistance, investing in silicone membranes ensures enhanced productivity and quality in your operations.
As businesses continue to evolve and seek effective solutions, embracing cutting-edge products like silicone membranes is not just an option—it’s a necessity. For companies looking to make the shift, exploring options from silicone-membranes.eu is the first step toward enhancing operational success and ensuring customer satisfaction.
Embrace innovation today with silicone membranes and witness a transformation in the efficiency and quality of your processes.