Understanding High Pressure Die Casting Mold
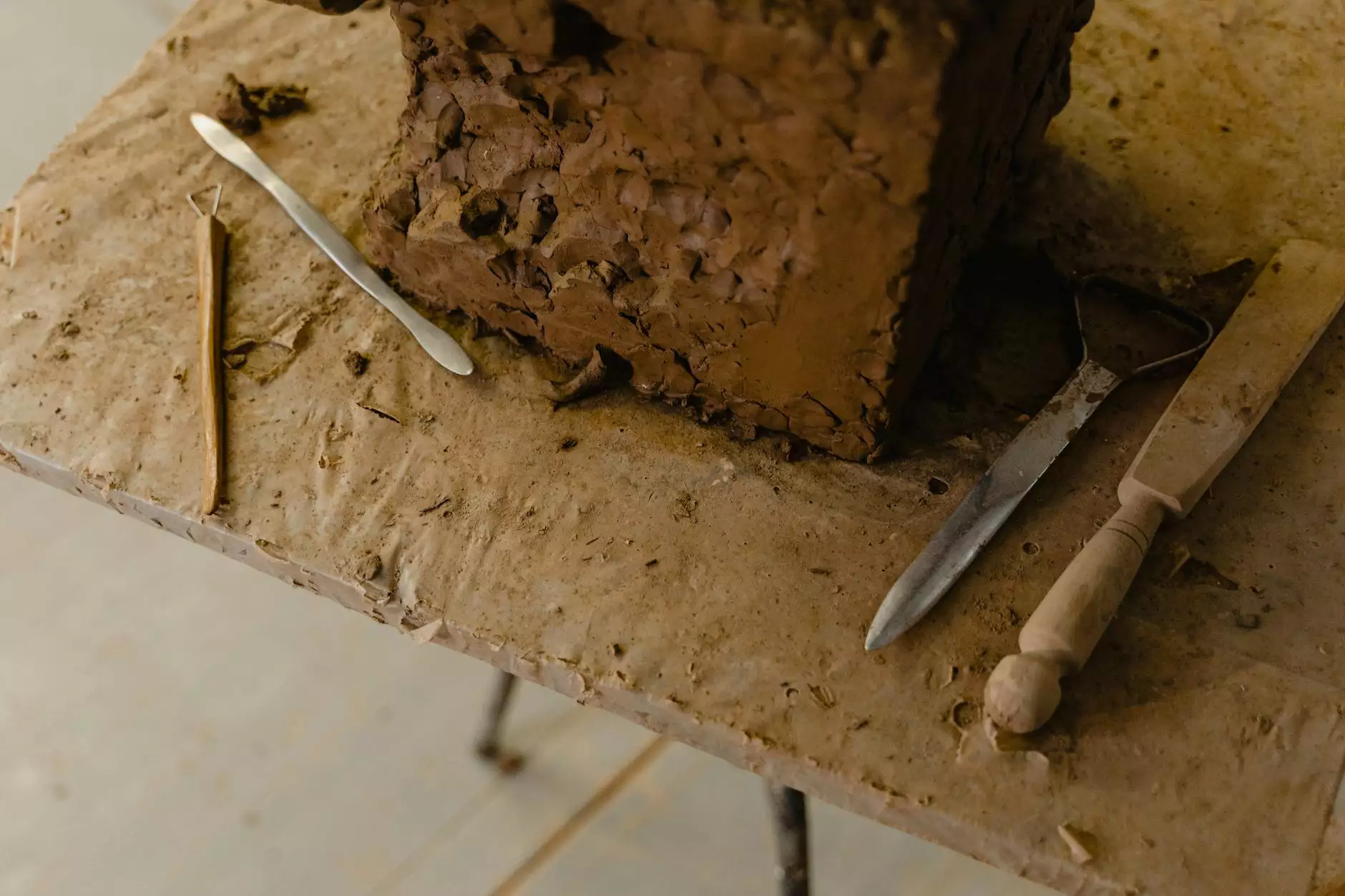
In the realm of manufacturing, the efficiency and precision of production methods are critical for achieving superior quality in end products. One such method is the high pressure die casting mold process, which has garnered significant attention in the field of metal fabrication. Through this article, we will delve deep into the intricacies of high pressure die casting molds, exploring their advantages, applications, design considerations, and how they have transformed the landscape of manufacturing.
What is High Pressure Die Casting?
High pressure die casting is a process where molten metal is injected into a mold cavity under high pressure. This technique allows for the production of complex shapes with high dimensional accuracy and a smooth surface finish. The process is predominantly used with non-ferrous metals such as aluminum, zinc, and magnesium, making it a cornerstone of the metal fabrication industry.
Process Overview
- Molten Metal Preparation: The first step involves melting the chosen metal, commonly aluminum or zinc, in a furnace until it reaches a liquid state.
- Injection: The molten metal is then injected into a steel mold (the die) at high pressure, typically between 1000 to 3000 psi.
- Cooling: Once the mold is filled, the molten metal is allowed to cool and solidify, taking on the shape of the mold.
- Mold Opening: After cooling, the mold is opened, and the cast part is ejected.
- Finishing: The finished parts may undergo various secondary operations to achieve the desired surface finish and mechanical properties.
Advantages of High Pressure Die Casting Mold
The adoption of high pressure die casting molds offers several advantages that modern manufacturers find invaluable:
1. Superior Dimensional Accuracy
Products manufactured using high pressure die casting typically feature remarkable dimensional stability. The high pressures used during the injection process minimize shrinkage and deformation, ensuring that components meet precise specifications.
2. Enhanced Surface Finish
The smooth surfaces of die-cast components reduce the need for extensive finishing operations, leading to lower production costs and faster turnaround times.
3. Design Flexibility
Metal parts can be designed with complex shapes not easily achievable through other manufacturing methods. This flexibility allows engineers and designers to innovate while still meeting strict performance criteria.
4. High Production Rates
The continuous nature of the processes involved facilitates high-volume output, which is particularly beneficial for mass production applications where efficiency is key.
Applications of High Pressure Die Casting Mold
High pressure die casting molds find their utility across various industries due to their inherent advantages. Some notable applications include:
- Automotive Industry: From engine components to transmission housings, the automotive sector extensively uses die-cast parts for weight reduction and improved fuel efficiency.
- Aerospace: Critical aerospace components often utilize die casting for their lightweight yet durable properties, thus enhancing overall vehicle performance.
- Electronics: The electronics industry relies on high pressure die casting for enclosures and components that require excellent thermal conductivity and electrical shielding.
- Consumer Products: Many everyday items, including kitchen appliances and tools, utilize die-cast parts due to their aesthetic appeal and functionality.
Design Considerations for High Pressure Die Casting Molds
When designing a high pressure die casting mold, several crucial factors need to be taken into account to ensure successful production:
1. Mold Design
The design of the mold must facilitate the smooth flow of molten metal while accounting for necessary features such as ejector pins, gates, and risers. Proper mold design minimizes metal turbulence and improves fill time.
2. Material Selection
The materials used for the mold must withstand high pressures and temperatures. Common materials include tool steel, which offers durability and resistance to wear.
3. Cooling System
An effective cooling system is critical to maintaining the temperature during casting and ensuring uniform cooling rates. This affects the quality and mechanical properties of the final product.
Challenges in High Pressure Die Casting
While the high pressure die casting process boasts numerous advantages, it also faces several challenges:
1. Tooling Costs
Initial tooling costs can be significant due to the complex nature of molds. However, these costs are offset by the high efficiency and low piece price in mass production runs.
2. Limited Material Choices
While non-ferrous metals are commonly used, the range of materials available for high pressure die casting is narrower compared to other methods, somewhat limiting versatility.
3. Thermal Management
Managing the heat generated during the process is crucial. Failure to do so can lead to defects or inconsistent qualities in the cast products.
The Future of High Pressure Die Casting
As industries demand higher quality, faster production, and greater efficiency, the future of high pressure die casting molds looks promising. Advances in technology, materials science, and automation are paving the way for innovations:
1. Automation and Robotics
Integrating robotics into the die casting process enhances efficiency and reduces labor costs. Automated systems can operate continuously, providing improved consistency in production.
2. Advanced Materials
The development of new alloy compositions may enhance mechanical properties, further broadening the capabilities of die casting.
3. Sustainability Initiatives
With rising environmental consciousness, innovations focused on reducing waste and improving energy efficiency are becoming a priority in metal fabrication technologies.
Conclusion
In summary, high pressure die casting molds represent a remarkable advancement in metal fabrication technology, offering substantial benefits in precision, efficiency, and design flexibility. As industries continue to evolve, the significance of this casting method will only increase, supported by ongoing innovations. For businesses and manufacturers looking to maintain a competitive edge, understanding and leveraging the advantages of high pressure die casting will be crucial in the years to come.
For more insights and information about high pressure die casting molds and other manufacturing processes, visit deepmould.net.